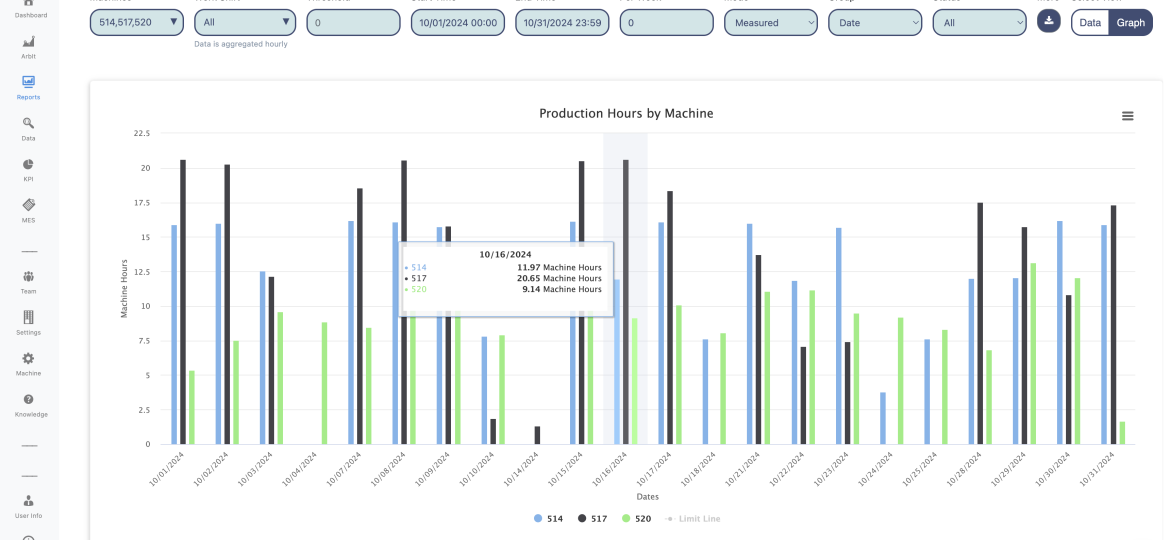
In today’s competitive manufacturing environment, staying ahead of the curve and growing your business means embracing tools designed to enhance efficiency, accuracy, and profitability.
Machine monitoring has become a game-changer in gaining transparency on multiple levels of the business and evaluating data to determine where they should focus their efforts.
To explore this topic, we sat down with SensFlo CEO and SoCal NTMA member Zakary Smith to chat through what manufacturers can do to harness the full potential of their data monitoring solutions—plus how SoCal NTMA can support their journey.
Why Does Machine Monitoring Matter?
Manufacturers have traditionally relied on pen-and-paper methods and software that requires manual input to track shop floor operations. While these approaches can present businesses with valuable insights, they can become time-consuming, tedious, and prone to error. In contrast, machine monitoring automates this process, delivering real-time, accurate information about machine performance and operational efficiency.
Why is this important? When manufacturing businesses have access to real-time data, they gain:
- Improved data accuracy
- Streamlined decision-making
- Enhanced operational transparency
The results are invaluable: maximized equipment utilization, faster issue resolution, and data-driven strategies that improve profitability.
The Value of Machine Monitoring
Some business owners are hesitant to invest in machine monitoring due to the associated upfront costs. However, there is so much value to be gained by leveraging accurate, up-to-date data, such as:
Maximizing Existing Equipment
By tracking machine performance on the shop floor, manufacturers can identify inefficiencies and uncover missed opportunities. For instance, idle alerts notify supervisors when machines are down so they can address maintenance immediately.
To address a common misconception, machine monitoring isn’t exclusive to the newest equipment on the shop floor. Zak explained a scenario where he visited a shop with equipment from the ‘40s that was effectively retrofitted to provide real-time data. So, even shops that don’t have the newest machinery can reap the benefits of machine monitoring.
Boosting Efficiency at Every Level
Machine monitoring provides actionable insights across all levels of the organization:
- Executives gain trust in the data they receive, enabling them to make informed decisions that advance the business.
- Supervisors can support their teams in real-time by addressing production bottlenecks as they occur.
- Operators benefit from increased transparency. When something goes wrong, there’s no more finger-pointing; data monitoring pinpoints the exact issue that occurred.
Driving Improvements Across the Organization
Real-time data allows manufacturers to assess machine throughput, validate efficiency rates, and inform time-based costing. This data isn’t limited to the shop floor; it can also connect with other datasets to inform pricing, scheduling, and more.
Reviewing Proactive Insights that Drive Quality
Monitoring factors like temperature, pressure, or cutting force can help identify process deviations before they result in defective parts.
Meeting Challenging Industry Requirements
Real-time machine monitoring is particularly helpful in sectors that require high levels of documentation, such as aerospace and medical manufacturing. With critical data in one consolidated space, companies can easily access the data they need to meet stringent industry standards.
How to Get Started
If you’re considering implementing machine monitoring in your shop, consider Zak’s recommendations:
- Audit your current infrastructure: Understand what equipment you have and what monitoring solutions are compatible.
- Collaborate with experts: Reach out to machine monitoring companies to explore your options.
- Engage with your peers: SoCal NTMA members, including suppliers and precision machining companies, can offer valuable insights based on their own experiences.
SoCal NTMA’s Role
When evaluating any type of innovation, lean into your SoCal NTMA community to listen, learn, and gain insights from professionals who understand the nuances of our industry:
- Community connections: Connect with your California manufacturing community and learn from peers who have successfully implemented machine monitoring in their facilities.
- Supplier insights: Lean into the cutting-edge technology solutions offered by our industry partners.
- Knowledge sharing: Tap into a wealth of expertise to determine the right solution for you and to ensure a smooth implementation.
As Zak from SensFlo puts it, “If you’re not measuring, you’re not growing.” Machine monitoring represents a significant step forward for manufacturers looking to improve efficiency and optimize production. With support from innovative partners like SensFlo and the collaborative manufacturing community of SoCal NTMA, manufacturers have the tools they need to thrive in the era of Industry 4.0.
Not a member yet? Contact us to start reaping the benefits of our illustrious network.