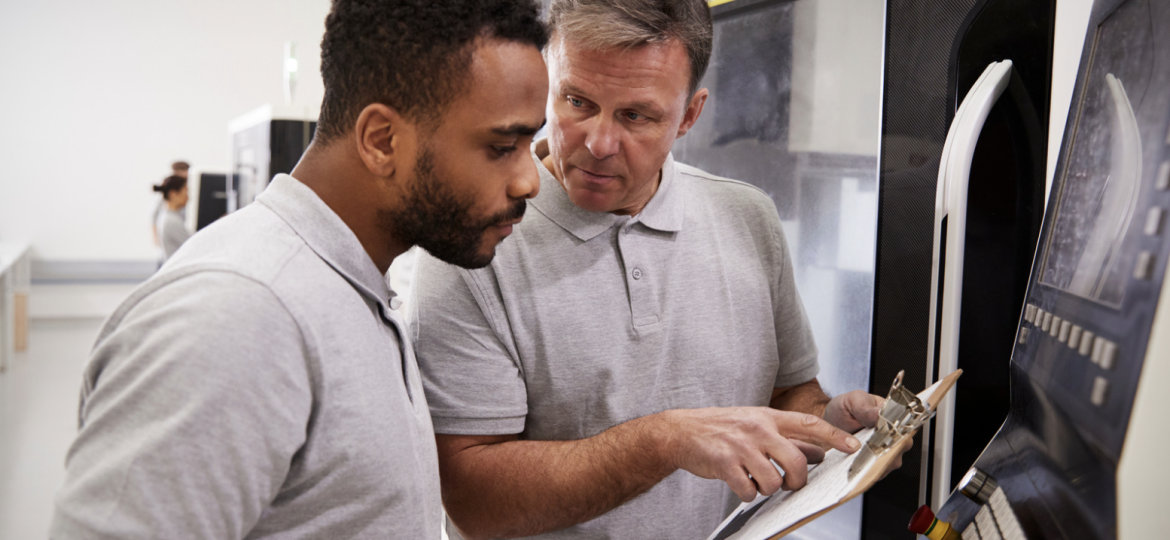
Our industry is evolving rapidly, driven by advancements in manufacturing technology and the shift toward Industry 4.0 and 5.0 practices. For manufacturers in Southern California, staying competitive means not only investing in state-of-the-art equipment but also cultivating a skilled workforce capable of working strategically and operating advanced systems.
Workforce development has never been more crucial to ensuring sustained growth and innovation in our field. That’s why SoCal NTMA is taking proactive steps to bridge the skills gap and strengthen workforce development initiatives. But this isn’t only a task for manufacturing organizations like us; members are also responsible for building the next generation of manufacturing professionals. Let’s explore some best practices for enhancing your company’s workforce development strategies.
1. Build Strong Relationships with Educational Institutions
One of the most impactful ways manufacturers can support workforce development is by partnering with local educational institutions. Southern California manufacturing companies have access to numerous community colleges and state universities with programs designed to train the next generation of industry professionals.
Hernan Ricaurte, President of Ricaurte Precision Inc. (RPI), has made workforce development one of the business’s key initiatives. One of his major strides: getting in the door at various schools in his region. According to Hernan, community colleges are doing a nice job of teaching students the fundamentals of precision machining. Still, it’s worth it for manufacturers to look into their curricula and meet the instructors. “These professors are solid people with strong backgrounds who are passionate about what they do. As future employers, we should be part of that, giving them support and building relationships with the future workforce.”
SoCal NTMA encourages our members to actively engage with these institutions by:
- Offering insights into modern manufacturing practices
- Helping develop internship programs
- Participating in curriculum planning to ensure programs align with industry needs
2. Develop an Enriching Internship Program
Many companies shy away from establishing internship programs due to the time and effort required to onboard and train interns. However, these programs offer significant benefits for manufacturers that adopt them, including:
- Exposure to emerging talent: Engaging with college-age students not only provides them with direct experience; it puts you in a great position should you decide to bring these interns on full-time.
- Internal process improvement: Sometimes, it takes an outsider joining your organization to see what’s going well and what could use improvement. Developing structured training programs for interns can prompt manufacturing companies to refine their operational processes.
- Mentorship development: Training interns encourages employees to become better mentors, fostering a culture of peer leadership and knowledge sharing.
3. Open Your Doors to Potential Talent
It’s not enough to stand in front of a lecture hall of students and tell them what modern manufacturing looks like; the real value comes from showing them what it looks like.
We encourage members to invite students to their facilities to experience firsthand:
- Automated production processes
- Digital ERP and QMS systems
- The advanced machinery that makes up your shop floor
While local schools are doing a fantastic job working with the resources they have, they understandably don’t have the latest models and brand-name equipment you have. Providing students with real-world exposure to the machinery they’ll be working with once they enter the workforce helps them better understand the skills required in today’s manufacturing environment.
4. Start Small
Running a manufacturing business is challenging enough, let alone adding another piece to the equation. Workforce development should undoubtedly be a priority to overcome any present and future hiring and upskilling challenges, but it takes time to develop a robust, sustainable program. Rather than diving headfirst, we recommend manufacturers take small steps to build their workforce development initiatives. Connect with a professor, invite a class for a shop tour, and then work from there.
5. Connect with Your Local Manufacturing Network
SoCal NTMA is pivotal in supporting our members’ workforce development efforts. By fostering connections between manufacturers and educational institutions, the organization ensures that the region’s manufacturing sector remains strong and competitive.
Through partnerships with groups like Network Kinection, which connects community college students with local employers, SoCal NTMA helps our members establish internship programs and tap into a pool of emerging talent. Some companies have already reported tremendous success from these collaborations! SoCal NTMA also supports grant programs for students interested in joining the manufacturing sector, providing financial assistance to those pursuing careers in our industry.
While our organization is making great strides to foster connections with emerging talent, our members are the ones driving these workforce development initiatives forward. If you’re trying to figure out where to start, talk to other members who have implemented internship and workforce development programs to learn from their experiences.
Not a member yet? Get in touch with the SoCal NTMA team to get started!